Machine monitoring provides a comprehensive view of real-time production metrics, a necessity for any company aspiring to maximize output. Utilizing machine monitoring software effectively transforms maintenance strategies for businesses that rely on heavy machinery. It addresses problems like component wear, overheating, or unexpected shutdowns before they lead to expensive downtimes
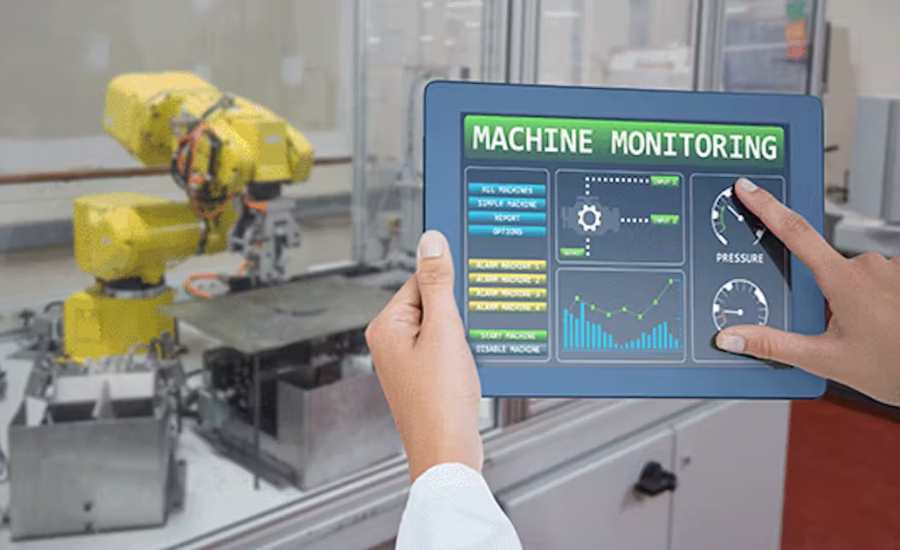
Understanding the Fundamentals of Machine Monitoring
Executing machine checking frameworks isn’t just about embracing new innovation — it’s tied in with helping productivity and smoothing out tasks. By diminishing the requirement for manual investigations and mystery, these frameworks prepare for an information driven way to deal with tasks.
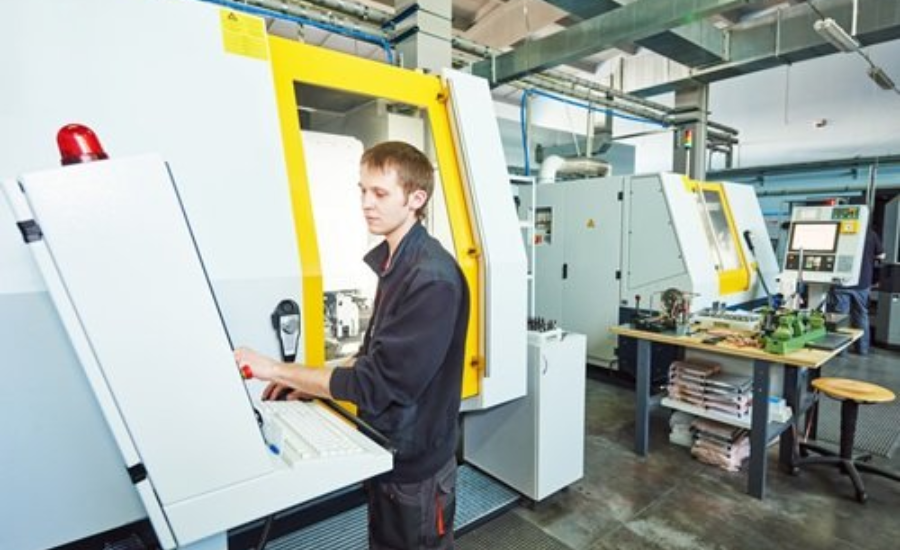
Machine observing changes modern upkeep by mixing flawlessly with existing work processes, guaranteeing industrial facilities run as expected. It’s tied in with responding to issues as well as foreseeing them, empowering organizations to take a proactive position in dealing with their tasks. The objective is to make an adaptable, responsive climate where organizations can adjust rapidly to changing creation requests or expected issues, remaining ahead in the present speedy modern scene.
How Machine Monitoring Systems Function
The essential objective of machine checking is to acquire an exhaustive comprehension of each and every part of the assembling system, giving you admittance to itemized creation information at the machine, plant, and undertaking levels.
Remarkably, just two or three sensors can capture over 100 valuable metrics, which are then turned into easy-to-understand reports. More importantly, this data provides a solid foundation for taking action.
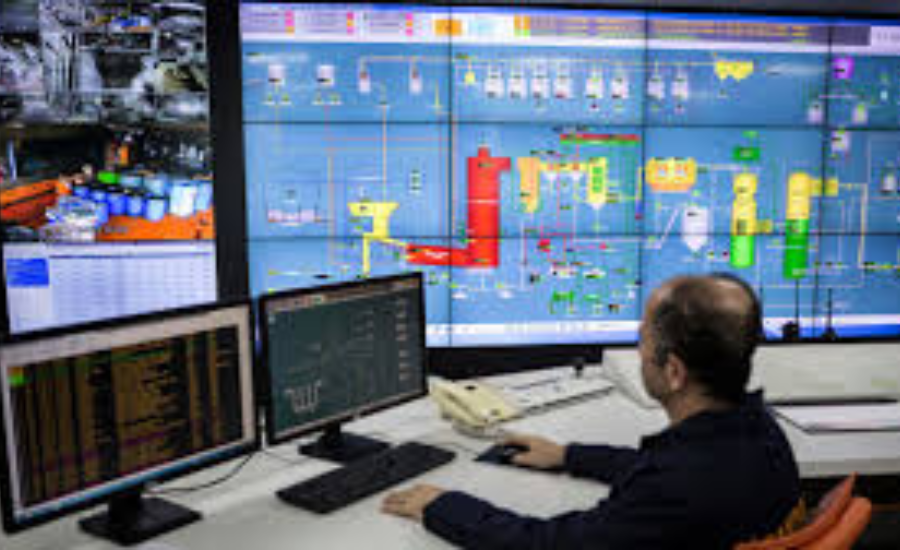
Managers, supervisors, and operators all play key roles in ensuring the machine monitoring system is used effectively, each contributing in their own way to optimize the system’s impact on the operation.
Why Machine Monitoring Matters
Machine monitoring brings significant value by shifting decision-making from guesswork to data-driven insights. When implemented correctly, it generates precise, objective data that can be easily translated into actionable insights. It makes a solid, single wellspring of truth, filling in as the establishment for a reasonable and powerful guide to further develop fabricating processes.
Top Advantages of Machine Monitoring Systems
Carrying out machine observing frameworks isn’t just about taking on new innovation — it’s tied in with helping productivity and smoothing out tasks. By diminishing the requirement for manual examinations and mystery, these frameworks prepare for an information driven way to deal with tasks.
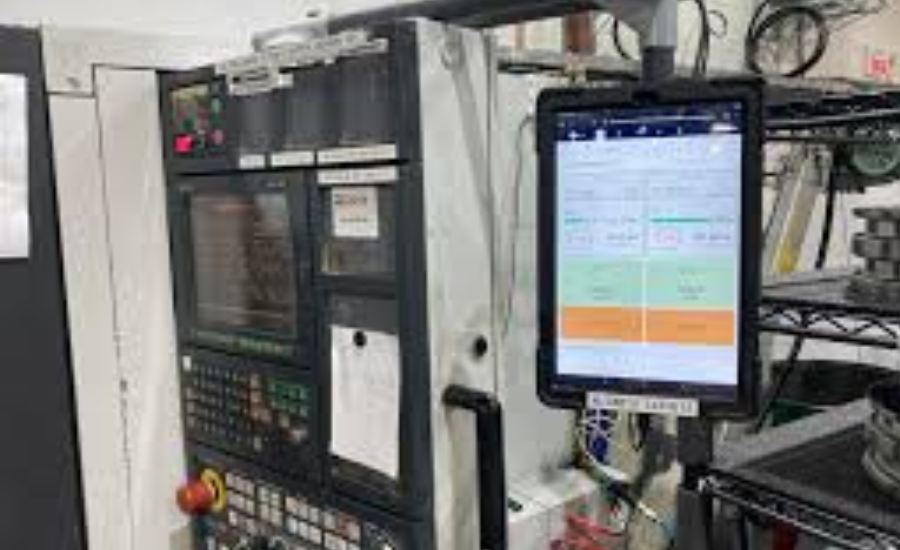
Machine checking changes modern support by mixing consistently with existing work processes, guaranteeing industrial facilities run as expected. It’s tied in with responding to issues as well as foreseeing them, empowering organizations to take a proactive position in dealing with their tasks. The objective is to make an adaptable, responsive climate where organizations can adjust rapidly to changing creation requests or possible issues, remaining ahead in the present quick moving modern scene.
Industries Leveraging Machine Monitoring Systems
Machine checking has turned into a fundamental apparatus across different enterprises, each with its own remarkable requests and difficulties. In the auto area, where accuracy and timing are basic, these frameworks guarantee sequential construction systems run as expected without interferences. By keeping up with top effectiveness, machine observing maintains the business’ severe quality norms and keeps creation plans on target.
In hardware fabricating, where even minor postponements can upset conveyance timetables, machine observing assumes a key part in enhancing tasks and guaranteeing items fulfill tight time constraints. Also, in the food handling industry, these frameworks are essential for keeping up with wellbeing and quality norms. By keeping hardware inside determined boundaries, they assist with forestalling tainting and guarantee items meet administrative prerequisites.
Drug organizations additionally benefit essentially from machine observing. Each snapshot of expanded functional effectiveness implies life-saving medications and medicines can arrive at the market quicker and all the more dependably. From accuracy driven ventures to those zeroed in on security and wellbeing, machine observing is changing the way in which organizations meet their objectives.
Advances in Machine Monitoring Technology
The mix of machine observing with arising advancements like the Web of Things (IoT) is reforming process enhancement. IoT helps gadget network, empowering ongoing information move and more exact following of machine execution. By utilizing IoT, organizations can computerize their cycles, lessening the requirement for steady manual management and permitting staff to zero in on additional essential assignments rather than everyday activities.
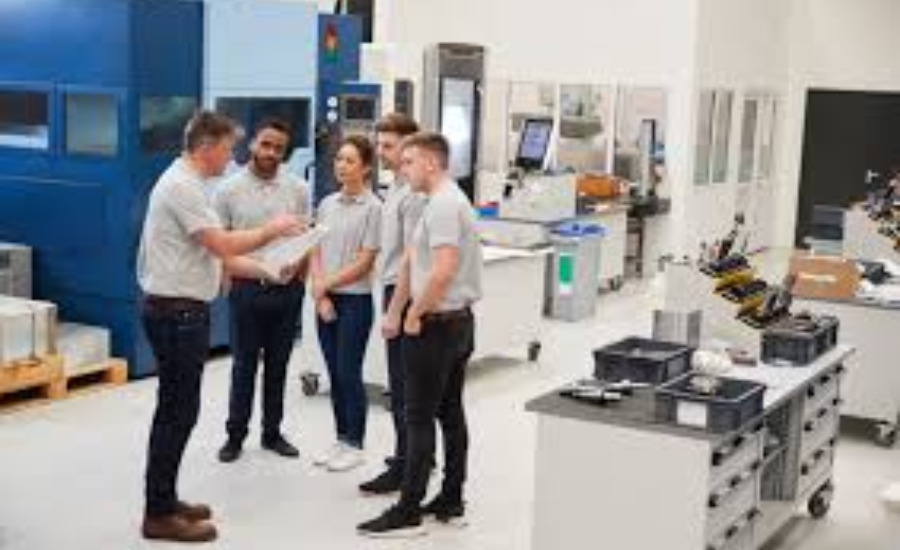
What’s more, developments like distributed computing and edge innovation are improving information handling capacities, making it simpler for organizations to deal with and examine huge measures of machine information. As handling power keeps on developing, organizations can acquire further experiences, recognizing even the littlest shortcomings. These mechanical headways advance current activities as well as future-evidence organizations, empowering them to scale and adjust their observing frameworks as their necessities and innovation develop.
Challenges in Implementing Machine Monitoring Systems
The mix of machine checking with arising innovations like the Web of Things (IoT) is upsetting interaction advancement. IoT helps gadget network, empowering ongoing information move and more exact following of machine execution. By utilizing IoT, organizations can robotize their cycles, diminishing the requirement for consistent manual oversight and permitting staff to zero in on additional essential errands rather than everyday activities.
Also, developments like distributed computing and edge innovation are improving information handling capacities, making it more straightforward for organizations to deal with and dissect immense measures of machine information. As handling power keeps on developing, organizations can acquire further bits of knowledge, recognizing even the littlest failures. These mechanical headways enhance current activities as well as future-confirmation organizations, empowering them to scale and adjust their observing frameworks as their requirements and innovation develop.
Data-Driven Measurements
Manual measurements are often susceptible to errors, and data collected by hand can be subjective. Machine monitoring, on the other hand, provides a reliable, objective way to assess machine performance accurately.
Real-Time Alerts
Machine monitoring systems are proactive, not passive. You can set them up to automatically alert a manager or technician if a specific threshold is exceeded. This helps prevent unnecessary machine damage and minimizes the risk of unplanned downtime, keeping operations running smoothly.
Equipment Health Monitoring
Upkeep timetables ought to never be taken a risk with. Unforeseen breakdowns and impromptu free time are exorbitant, and think about when issues will emerge can be unsafe.
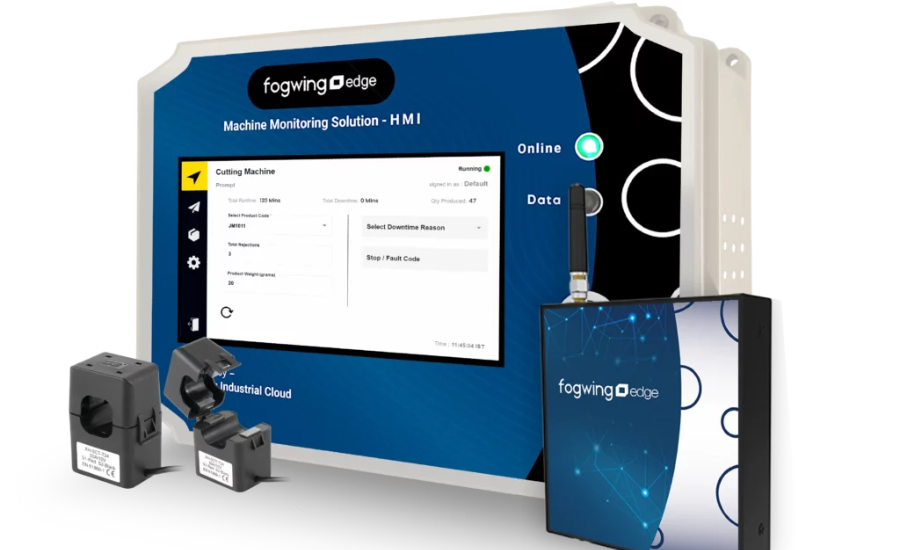
Machine checking permits you to follow the state of each machine, giving a more profound comprehension of the whole lifecycle of parts and resources. Sensors can quantify continuous information on factors like vibration, temperature, clamor, and part dislodging, which helps screen the mileage of mechanical parts.
You can likewise watch out for natural circumstances in your office. For instance, in the event that the processing plant is excessively sticky or heat isn’t dispersing as expected in a specific region, these variables can add to untimely machine wear. Without the right information, it’s almost difficult to pinpoint the underlying drivers of these issues.
Condition checking is significant for advancing support plans and acquiring knowledge into how machines are acting in your particular climate. By gathering information on machine wellbeing and execution progressively, machine checking lays the basis for successful prescient upkeep programs, assisting you with remaining in front of likely issues before they become serious issues.
The Future of Machine Monitoring Systems”
The future of machine monitoring holds exciting potential. By integrating artificial intelligence (AI) and machine learning (ML), predictive capabilities will be taken to the next level. These technologies can analyze complex data patterns, empowering industries to make more informed decisions, optimize efficiency, and drive innovation.
For example, AI advancements are poised to transform how companies predict machine failures, reducing unexpected downtime even further than current methods. As technology continues to evolve, machine monitoring will be central to shaping the future of industrial operations. Businesses that embrace these innovations will lead the way in efficiency and innovation within their industries.
Final words.
All in all, machine checking isn’t simply a device — it’s an extraordinary power reshaping the manner in which enterprises approach proficiency, upkeep, and development. By utilizing continuous information, prescient investigation, and arising advances like computer based intelligence and AI, organizations can improve tasks, lessen personal time, and expand the life expectancy of basic apparatus. As the scene keeps on advancing, the people who take on machine observing won’t just remain in front of the opposition yet will likewise make way for the fate of modern greatness. An opportunity to embrace this change is currently, and the advantages are clear: a more astute, more proficient, and more maintainable future for all ventures.
Visit our site for more information about Machine Monitoring.Thanks